OUR EXPERTISE
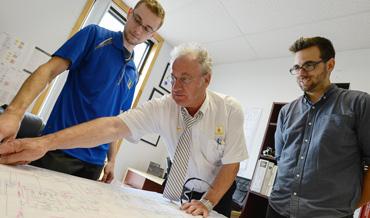
DESIGN
We have the Design Engineering experience to analyze and solve your most difficult hydraulic or mechanical problems with a full time staff of professional engineers, designers and technicians.
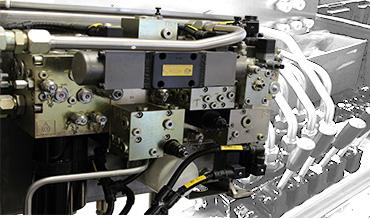
MANUFACTURING
We fabricate and assemble all of our designs in-house. Our repetitive manufacturing facility assembles high quality tested OEM products to a broad customer base across multiple industries.
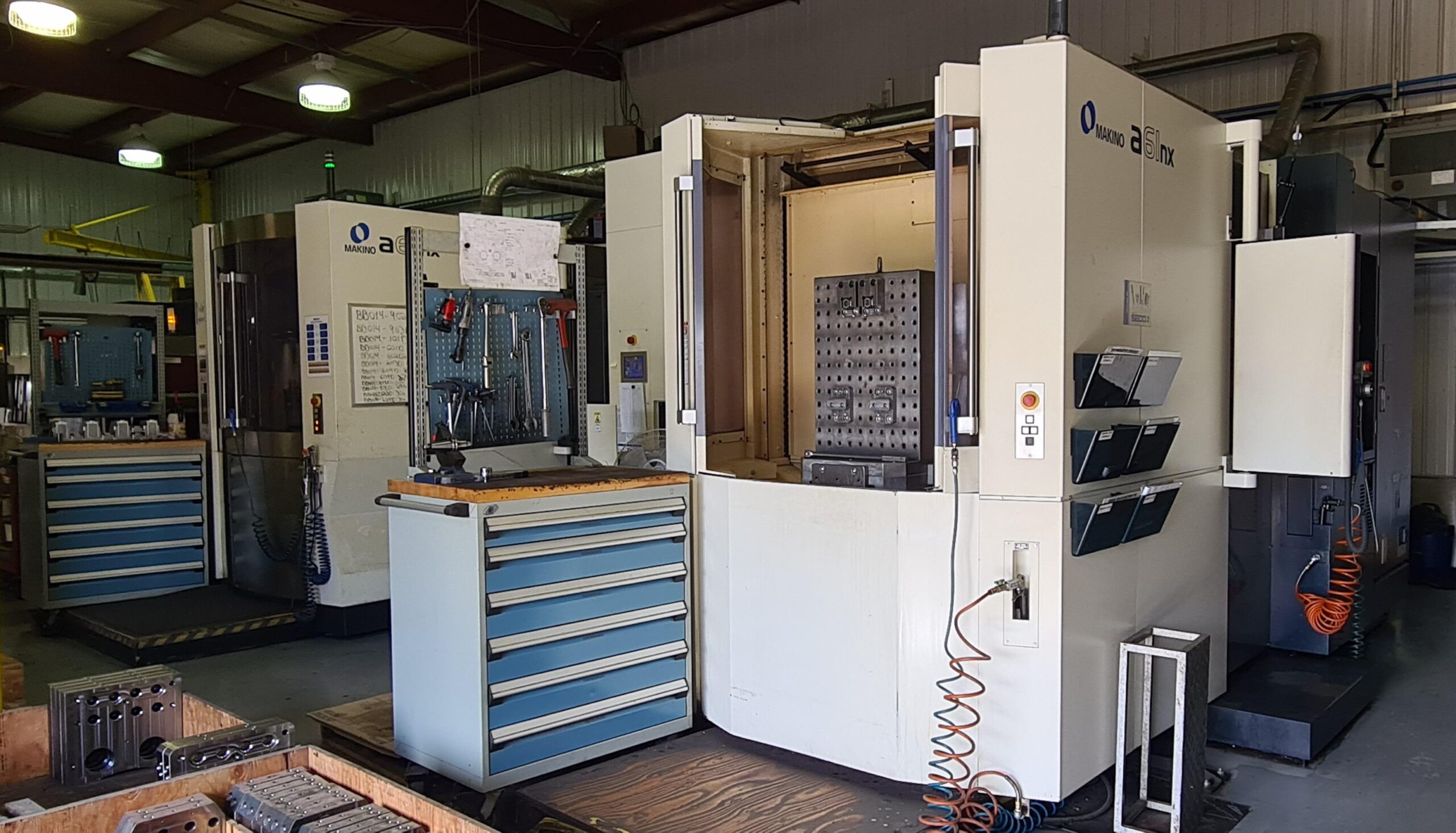
MACHINING CENTER
With our modern tools and highly efficient team Hydrep offers unparalleled machining service.
SOLUTIONS
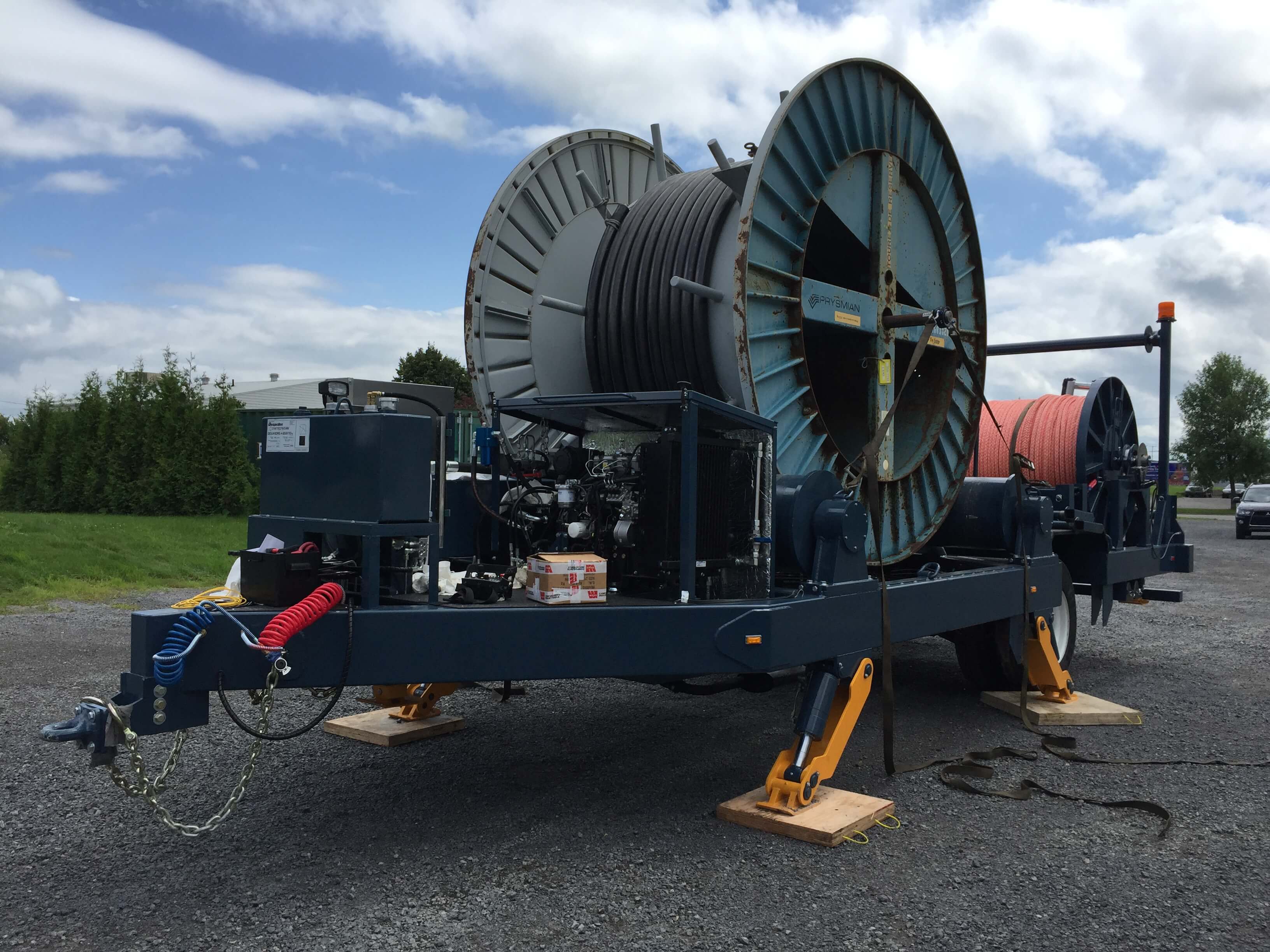
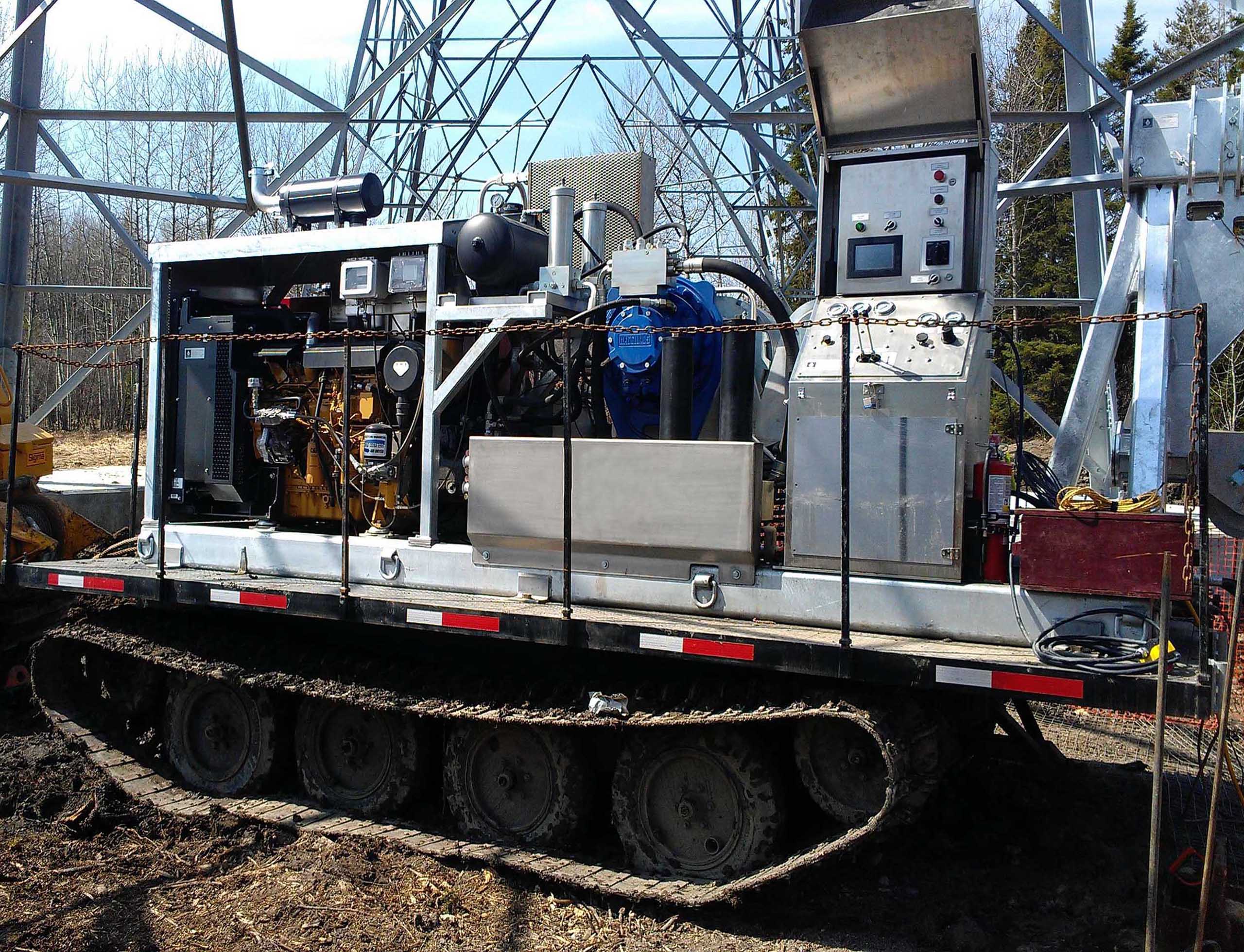
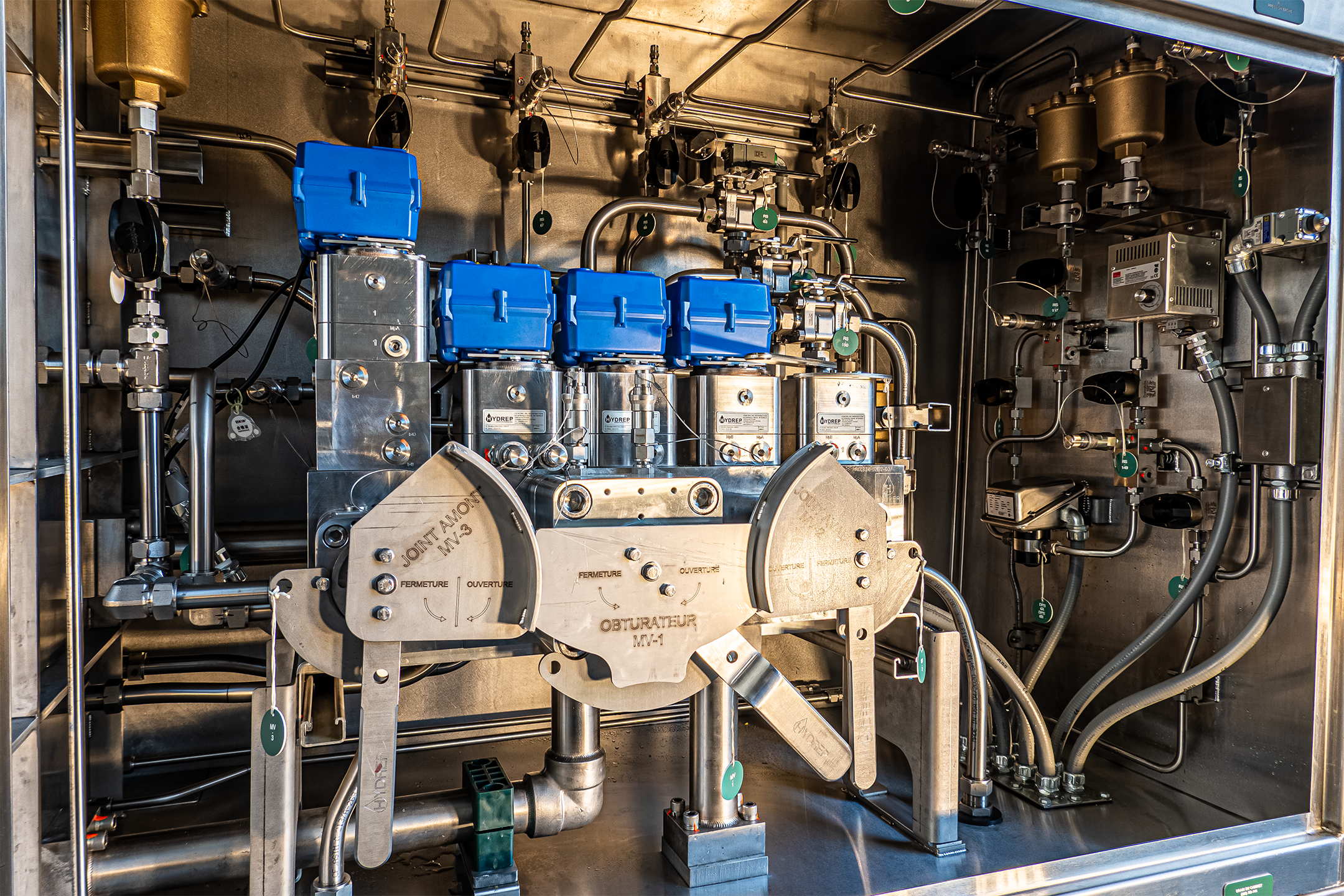
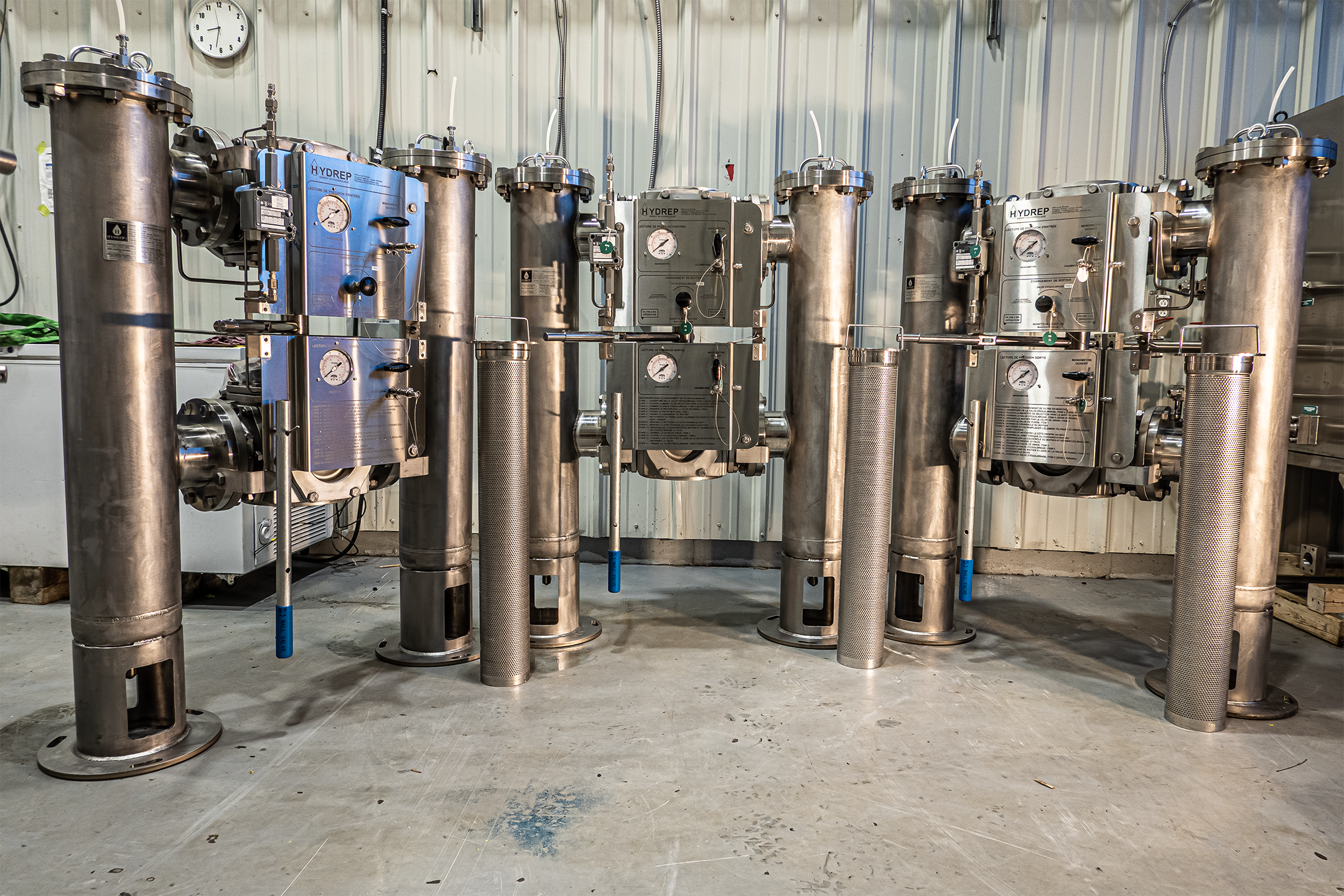
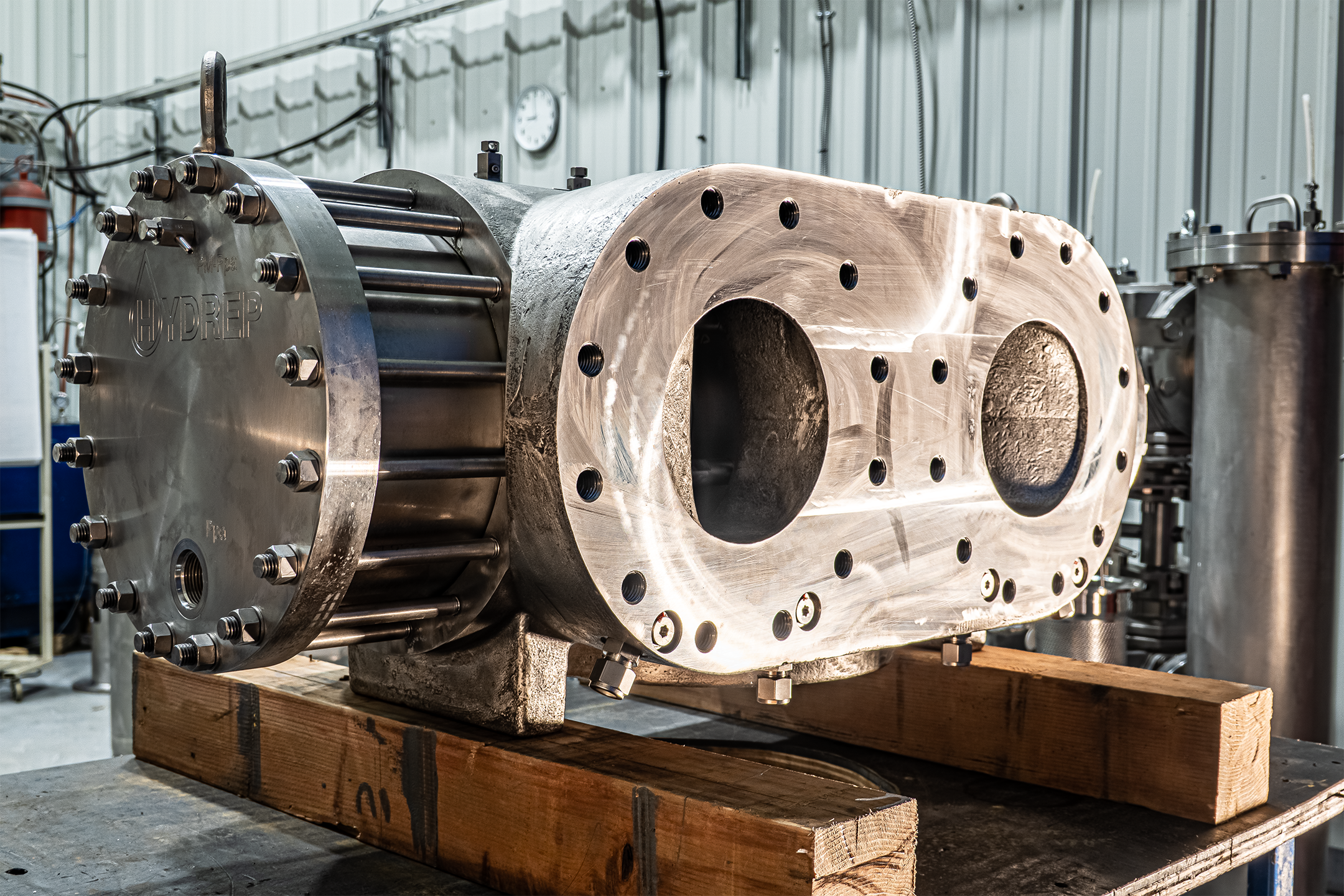
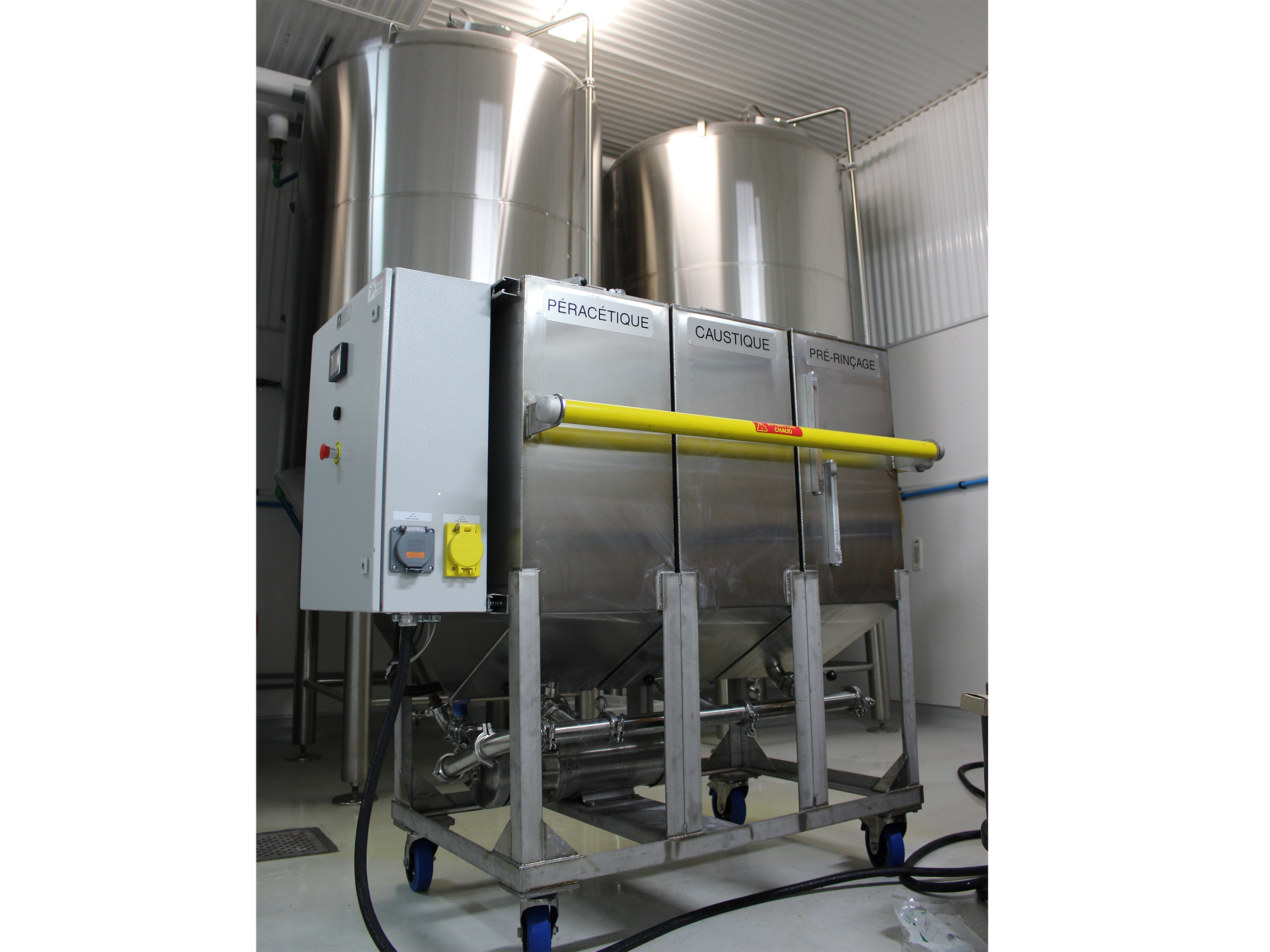
ISO 9001: 2015, 14001: 2015, CWB, ASME, RBQ and Controlled Good Program certified company
ISO 9001: 2015 established the requirements for a quality management system. It helps companies and organizations to gain efficiencies and increase customer satisfaction. CSA W47.1 is a fusion welding of steel company certification.
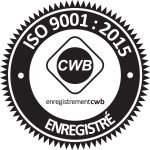
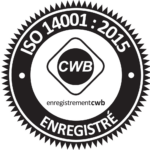
SECTORS
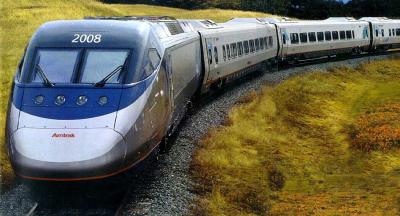
TRANSPORT
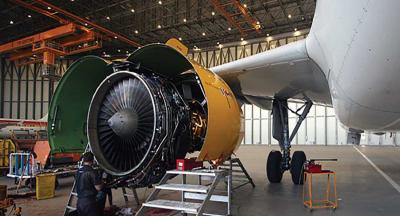
AERONAUTICS
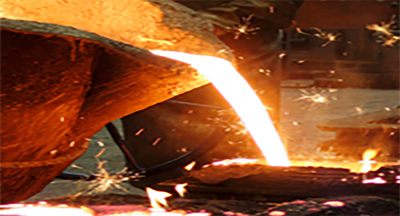
PRIMARY METAL PROCESSING
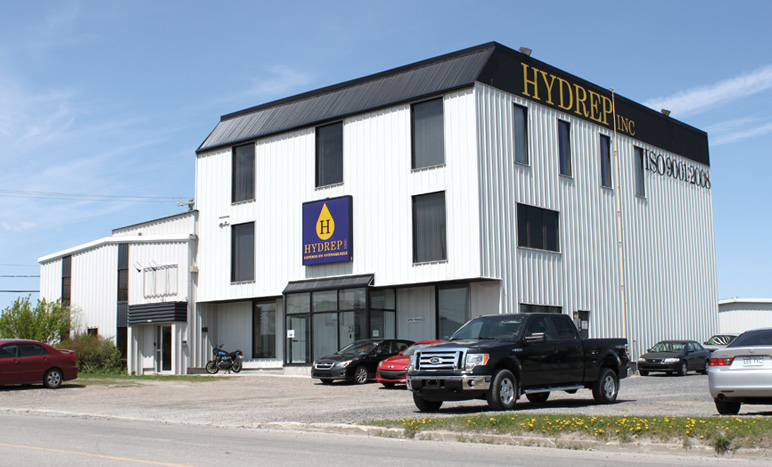
ABOUT US
Hydrep thinks, designs and manufactures prototypes and serial products for all fields of electro-hydraulic applications.
Our engineers, technicians, designers, machinists and skilled engineers provide the expertise of our company.
Hydrep has the motivation to build HERE and export its expertise around the world.
CONTACT US
Phone
Address
EMERGENCY
QUESTIONS,COMMENTS
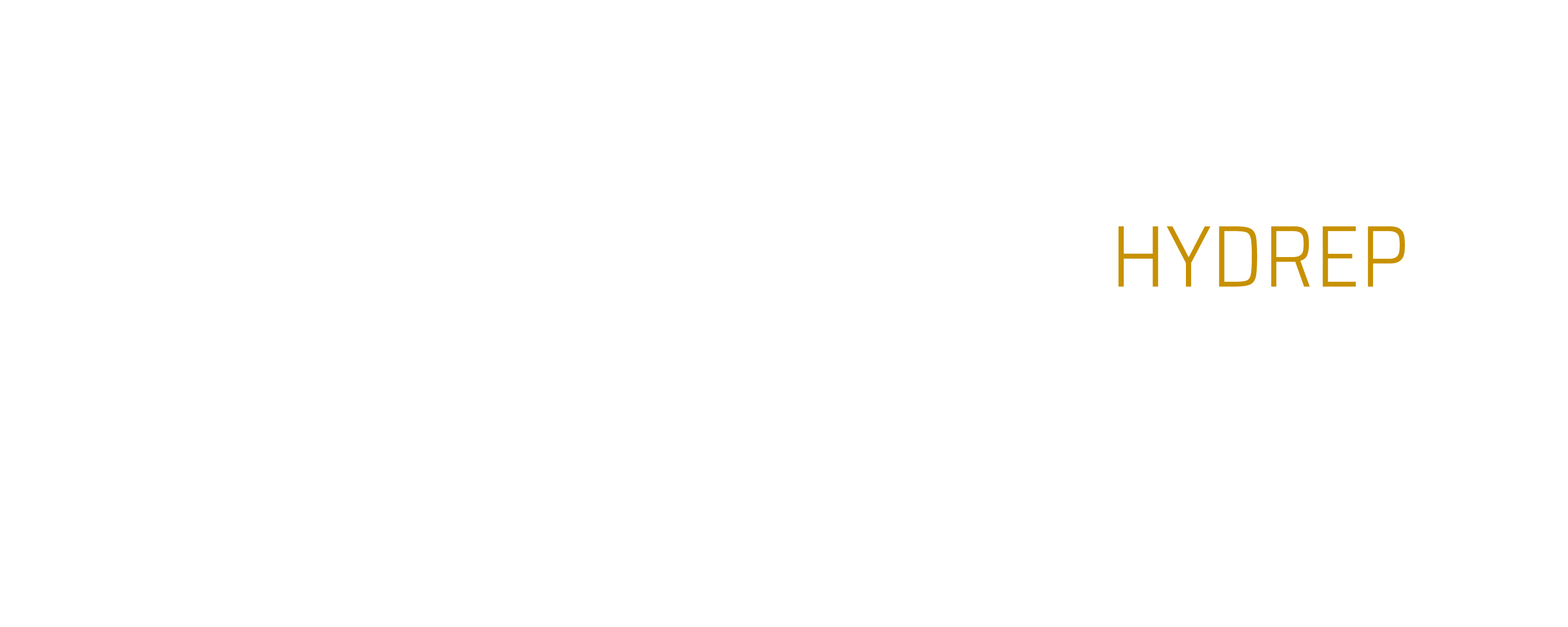